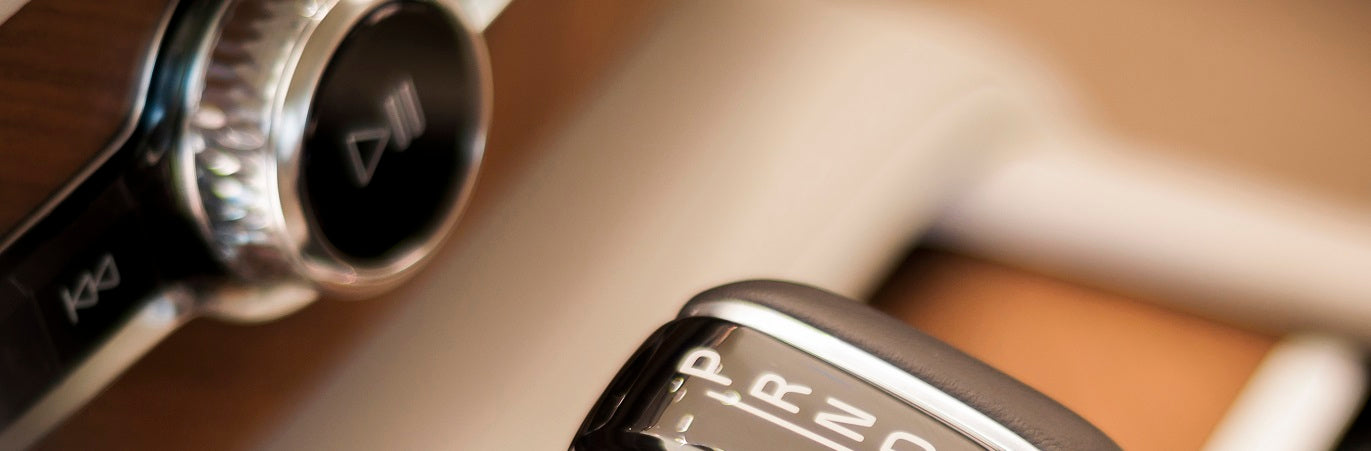
Vehicle Interior Noise Testing
Vehicle Interior NVH Testing
Vehicle interior noise, vibration and harshness (NVH) involves a number of different tests – all related to noise inside the vehicle originating from road, body, chassis and components of the vehicle.
The main focus areas are:
- TOTAL INTERIOR NOISE
A way of testing the general experience of a vehicle’s acoustic comfort. - ROAD NOISE
Testing related to how road excitation contributes to the interior noise both structure-borne and airborne – depending on well-defined road surfaces and tires. - THE SOUND PACKAGE
An area that affects most of the NVH areas. - COMPONENT NOISE
Concerns all additional systems like the heating, ventilation and air conditioning (HVAC) system, power windows, etc. These are mostly electrical or driven by the engine belt, and sometimes hydraulic. Read about electric applications here. - BRAKE NOISE
A chassis-related noise and a big problem for car manufacturers. - COMPUTER MODEL VALIDATIONS
Testing on prototype parts or vehicles.
Learn more about the challenges and how to select the right microphone
Selected products
- GRAS 146AE
The ideal, free-field microphone for almost all acoustic NVH testing - GRAS RA0357
Corrector enabling use of 146AR in a random-incidence sound field - GRAS 42AG
The ideal solution for calibration - GRAS 46BC
The only true multifield, high-sensitivity 1/4" microphone - GRAS 46BL-1
Resources
Vehicle Interior Noise on Electric Vehicles
Measuring inside the cabin is more challenging on an EV compared to an ICE. A main reason for this is that the general increase in high-frequency content will make it more difficult to do TPA/ENR types of measurements. Many sound sources have very limited energy at 20 kHz which makes transfer path analysis from the engine bay more difficult.
Many EVs/HEVs use a more distributed powertrain with individual electric engines. This in combination with wind/road/tire noise, which are all dominant noises, makes it more relevant to use pressure microphones instead of directional free-field microphones in the cabin.
Active noise cancellation: The phase is very hard to control inside the cabin – and if not controlled, it can instead amplify the noise.
Passive noise cancellation: Traditional ways of vehicle noise cancellation such as acoustic package and anti-vibration mounts will still be used for EVs/HEVs. It therefore needs to be adjusted to the new environment.
We recommend to use a low-noise type microphone like e.g. GRAS 47HC ½” CCP Low-noise Microphone System. Another option is to use GRAS 147AX CCP Rugged Pressure Microphone, which has a unique mounting system, MagMountTM, ensuring precise repeatable tests in the cabin in combination with driver seat measurements using GRAS 146AE ½” CCP Free-field Microphone Set.
See our complete application offering within electric vehicles here.
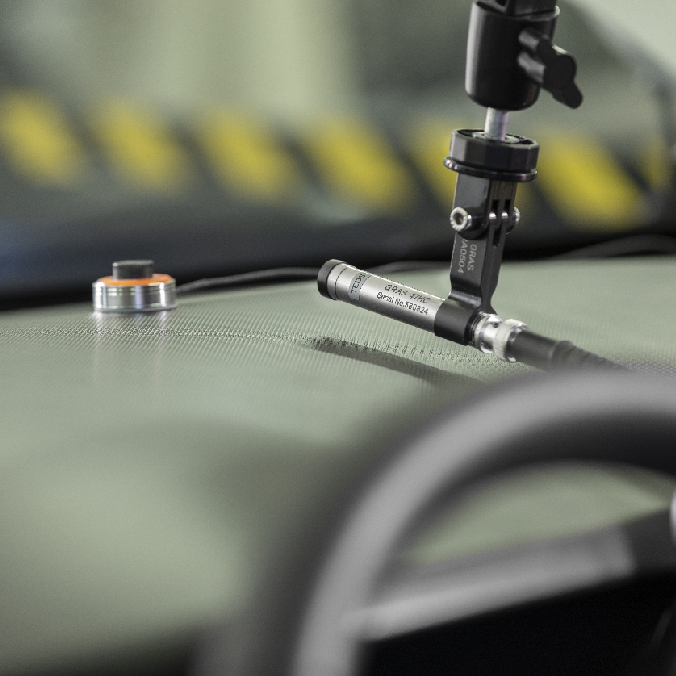
ACOUSTIC TEST TYPES WITHIN VEHICLE INTERIOR NVH TESTING
Total interior noise is a good measurement for benchmarking and a measurement often used by automotive magazines for comparison of different car models. It concerns the overall noise level inside the vehicle at its full speed range and is a way of testing the general experience of a vehicle’s acoustic comfort.
Articulation Index (AI) is often used as a good index for sound insulation and sealing as well as speech intelligibility.
Road noise is one of the most annoying interior noises in a vehicle. Road excitation contributes to the interior noise both structure-borne and airborne. Requirements are normally based on subjective evaluation, benchmarking and experience. The requirements include noise level and frequency balance. Extra focus is on tire cavity resonance noise around 200-250 Hz and tread noise.
The sound package is closely related to most of the NVH areas. The first step is to make sure that the body is sealed as much as possible. This reduces high-frequency leakage and increases the overall NVH performance. Structural damping and heavy-layer isolation mats must be optimized for best performance and lowest weight and cost. Finally, acoustic absorption material at critical locations is used to improve the acoustic interior comfort.
Component noise is often divided into two areas: customer-actuated sounds and system-actuated sounds. Customer-actuated sounds are directly related to an action like opening or closing a door or power-operating windows and will likewise provide user feedback. System-actuated sounds are controlled independently of any action from the driver or passengers and the reason why the sound is not always easy to understand. The HVAC system is one of the dominating noise sources in the vehicle during cool down or heat up and needs a lot of careful design work.
Brake noise is a chassis-related noise and an area of great concern for OEMs across the world. The noise is caused by friction-induced vibrations, which make the brake system radiate noise. This will in turn cause a lot of irritation and disturbance to the car owner and any person near the vehicle when it occurs. The brake noise can lead to poor results in surveys of customer satisfaction and high warranty costs. Therefore, the development of brake systems with minimum noise issues are highly prioritized in the automotive industry. Brake noise is a very complex problem and the research in this area is in continuous progress.
On top of that, the electrification of vehicles requires new brake design as well as increased focus on noise since the auditory masking from the engine disappears. However, the traditional brake systems will be used to a lesser extent in an electric vehicle. A regeneration process takes place during deceleration used to provide battery charging which in many cases will be sufficient to control the vehicle speed without using the brake pedal. Read about electric applications here.
Three test levels
It is important to develop validated test procedures that are fast and easy to perform, and it is good practice to use a standardized selection of transducer types and transducer positions to be able to run several tests efficiently at the same test time. These procedures should also be as generic as possible to allow variation of system design. The engineers need to stay updated on new concepts and perform benchmarking.
Tests are performed at three main levels, vehicle test, system test and component test. Computer model validations can be an integral or separate part of these tests. The tests are used for development, requirement verification, troubleshooting and computer-aided engineering (CAE) correlations.
Vehicle test
A vehicle verification test typically includes two to four microphones at ear level inside the vehicle distributed between the driver’s and passenger seats. The test conditions are specified in detail. Tests are performed both on test tracks, on a NVH chassis dynamometer, in the NVH laboratory or in a hemi-anechoic test cell.
Vehicle testing involves testing a range of noise generating sources:
- The total interior noise test is performed on a smooth road test track while accelerating from low to high speed. The test also includes analysis of sound pressure level (SPL) and AI versus speed.
- Road noise is tested at dedicated NVH test tracks with well-defined road surfaces like smooth, coarse or grooved. Analysis of SPL, third octave band spectra, narrow band spectra and AI is done at different vehicle speeds. External microphones or intensity probe with windshield can be used for measurement of near-field tire noise.
- Sound package testing at vehicle level is done indirectly by the vehicle tests.
- Component noise is tested during typical usage conditions, but isolated with no other sounds. The tests are performed in a vehicle in a hemi-anechoic test cell.
- Brake noise is evaluated with microphones at ear level and in the wheelhouse while driving on a dedicated test route with all possible braking and different environmental conditions.
System test, acoustic transfer function (ATF)
System testing requires the usage of a lot of different acoustic sensors. These tests are mostly performed in a NVH laboratory, either with a complete vehicle or for a system or component only.
System/component level test examples include:
- ATF from engine bay to interior to verify sound package. Noise transfer function (NTF) test to measure the structural noise paths. These tests are done with the vehicle in a hemi-anechoic test cell.
- Noise source contribution from different surfaces like floor, dashboard and doors is measured with a microphone or intensity probe. This can be done for a full vehicle in the laboratory on a NVH chassis dynamometer or using speakers as noise source, but also on a test track. An acoustic camera can also be used to locate noise sources and detect leakage. Subsystems like a vehicle front structure or door system are installed in an anechoic/reverberation suite, and the contribution from different areas is measured with a sound intensity probe. These tests are used for optimization of the panel treatment.
- Sound absorbtion and sound transmission loss (STL). The properties of the acoustic materials used in the sound package are tested in the NVH laboratory. Sound absorption coefficient is tested in a reverberation test cell or in an impedance tube. STL is tested with the test object installed in an anechoic/reverberation suite. The reverberation chamber acts as the diffuse sound source, and the STL is calculated from measurements of the SPL in the reverberation chamber as well as the sound intensity in the anechoic chamber.
Component test
Component testing also requires the usage of many different acoustic sensors. As with the system test, these tests are mostly performed in a NVH laboratory with a complete vehicle or for a specific system or component.
Component noise testing include:
- Component noise at system level, like the blower noise of a complete HVAC module or the operating sound of an electric sunroof module, is tested in an anechoic or hemi-anechoic test cell. The system is operated at correct operating conditions, but not the correct boundary conditions to the vehicle.
- Separate components of a system, like a small electric motor or solenoid, are also tested in an anechoic or hemi-anechoic test cell and under as valid operating conditions as possible. SPL or sound power and frequency, or order analysis as appropriate, are used to detect the noise corresponding to the component.
- Brake squeal noise is tested at system level for a full vehicle corner in a dedicated brake squeal dynamometer.
Computer model validation
A lot of the design decisions and verifications are done before any prototype part or vehicle is manufactured. The body and chassis design has a big impact on vehicle NVH performance, especially for powertrain and road noise, and needs to be verified at an early stage. Measurements from existing cars or systems are used to correlate the simulations. Mule vehicles (existing cars modified with new concepts) are also used.
General measurements include modal analysis and transfer function measurements, NTFs and ATFs. Impact hammer, shakers and volume velocity sources are used for excitation. Furthermore, the standardized vehicle verification tests are used for computer-aided engineering (CAE) model verification.