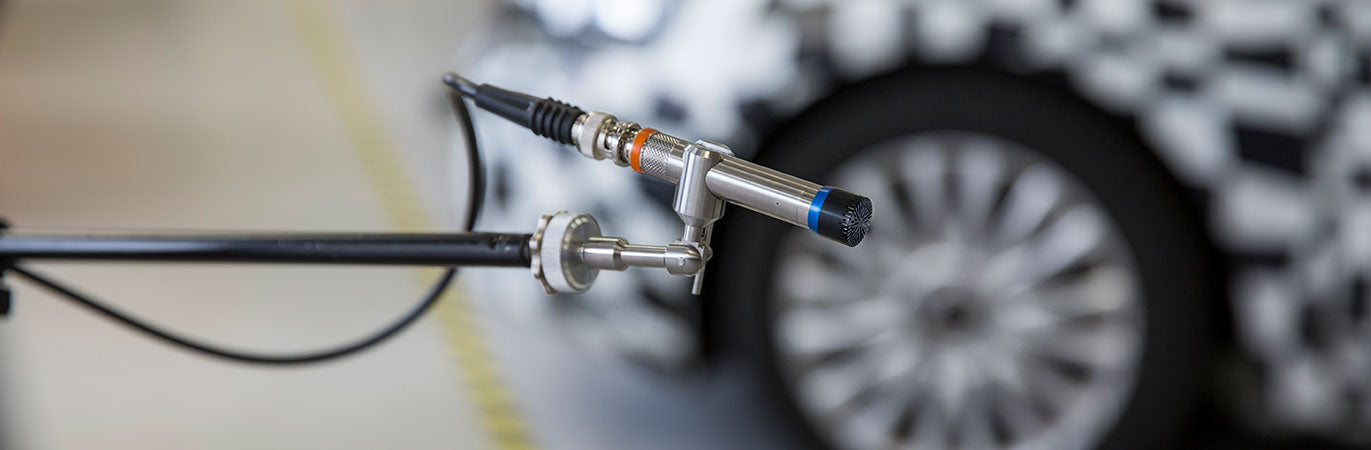
Powertrain Noise Testing
Powertrain NVH testing
Powertrain noise, vibration and harshness (NVH) testing concerns the overall driver experience of the vehicle propulsion system, and this includes everything that makes the vehicle move. The noise level and sound quality are both very important since some parts of the sound provides important feedback to the driver while other parts are just annoying. The noise from all these sources, i.e. the internal combustion engine (ICE) with air induction, exhaust system, tail pipe, gear box, belt drive system, pumps and accessories like cooling systems and fuel pump is transmitted both airborne and structure-borne into the vehicle and contribute to the vehicle acoustic comfort. The powertrain noise also affects the external noise (the pass-by noise), which is regulated by legislation.
Vehicle interior measurements form the basis for the verification of the vehicle NVH performance. The measurement procedures are developed to provide results that correlate with subjective ratings that are used as customer satisfaction references. Development measurements in the engine bay will provide detailed information about noise source location, source strength, frequency content, engine order content and time variation, and this will explain the physical cause of the noise. The results of all these tests will guide the engineers how to reduce unwanted noise.
Engine bay measurements in combination with interior or exterior measurements will provide information about the performance of how well acoustic packages work. These packages provide sound insulation or sound absorption. The measurements are done both on the OEM’s development test vehicles and on the production follow-up vehicles as well as for benchmarking to make sure that the customer’s expectations for a new vehicle can be fulfilled.
Learn more about the challenges and how to select the right microphone
Selected products
- GRAS 146AE
The perfect choice for inside car testing - GRAS 147AX
A rugged surface microphone with an ingenious mounting system for repeatable cold and hot engine testing – also on the proving ground - GRAS 42AG
The ideal solution for calibration
Resources
Powertrain Noise Testing on Electric Vehicles
Even though powertrain noise is drastically reduced on EVs/HEVs, other noise sources become annoying and new frequency content is unmasked.
In general, the sounds in an EV are dominated by complex high-frequency tonal components.
Some hybrids have the E-motor connected via the existing gearbox. Other EV platforms have different needs for gearing. Due to the form factor of the E-motors, the gearbox is placed differently than in a typical ICE platform, resulting in a more complex noise environment because the noise is coming from new source locations.
We recommend low-noise microphones such as GRAS 47HC ½”CCP Low-noise Microphone System or GRAS 40HL ½” LEMO Low-noise Microphone in combination with GRAS 146AE ½" CCP Free-field Microphone Set.
See our complete application offering within electric vehicles here.
ACOUSTIC TEST TYPES WITHIN POWERTRAIN NVH TESTING
It is important to develop validated test procedures that are fast and easy to perform, and it is good practice to use a standardized selection of transducer types and transducer positions. The main tests include sound pressure level (SPL) and order content from the powertrain at different load conditions like drive away, steady state, acceleration, part load and maximum load (WOT). The tests are performed both for the engine separately in an engine NVH test cell and for full vehicle integration tests on a NVH chassis dynamometer or on road*.
Complementary vehicle measurements in the engine bay area includes:
- Near-field measurements close to the different sources
- Far-field measurements for sound power estimations
- Sound intensity measurements
- Microphone arrays for sound source location
- Acoustic transfer function measurements (ATF)
When testing transmission noise, the verification of the gearbox design is tested in a NVH drivetrain test rig where noise emissions and vibrations at the interfaces to the engine can be investigated. Furthermore, the vehicle integration is verified with the complete car driven on a NVH chassis dynamometer or on road.
The transmission noise from manual or automatic gearboxes must be low. Gear whine originates from gear meshing and often produces high frequencies where less masking from other sounds help. Gear rattle noise is another issue. The actual design of the gears like shape, material and tolerances is critical, and transmission error is the most important design criteria.
Computer model validation
A lot of the design decisions and verifications are done before any prototype part or vehicle is manufactured. The body and chassis design thus has a big impact on the vehicle NVH powertrain performance and needs to be verified at an early stage. Measurements from existing cars or systems are used to correlate the simulations. Mule vehicles (existing cars modified with new concepts) are also used.
General measurements include modal analysis and transfer function measurements, NTFs and ATFs. Impact hammer, shakers and volume velocity sources are used for excitation. Furthermore, the standardized vehicle verification tests are used for computer-aided engineering (CAE) model verification.
*) For more information on other NVH powertrain testing applications, please refer to other automotive application literature from GRAS
Example
A vehicle verification test on a NVH chassis
dynamometer typically includes two to four
microphones at ear level inside the vehicle
distributed between the driver’s and passenger
seats. The wheel rpm is used to track the gear
orders and can be registered with an optical or
inductive sensor or from ABS sensors. The CAN
bus also provides powertrain performance data
to further increase the knowledge