
Buzz, Squeak and Rattle Noise Testing
Buzz, squeak and rattle are all noises produced by parts installed in such a way that they create annoying sounds. Buzz, squeak and rattle is thus caused by the relative motion between installed parts, which make them interact, sometimes only at certain environmental conditions.
More precisely, buzz originates from the structure or part itself, squeak is caused by friction between parts, and rattle is caused by impact. Buzz, squeak and rattle is a well-known source of extreme annoyance to the driver and the reason for many customer complaints and is an important part of the overall perception of a vehicle. Even if the sound levels are low, buzz, squeak and rattle noise is often audible due to its intermittent character and often includes a sound with a frequency content where sound masking is low. A vehicle without buzz, squeak and rattle is associated with high quality, which is why it is important for OEMs to achieve this. Masking levels are set lower and lower, especially in electric vehicles, but at the same time the demand for less weight increases the design problems when it comes to preventing buzz, squeak and rattle noise. Read about electric applications here.
Chassis and structural design, material selection and controlled tolerance chains are all important elements to consider in order to avoid buzz, squeak and rattle noise. This must be specified in the design targets and design guidelines all the way from prototype to production, and should constantly be measured with reliable measurement microphones.
Learn more about the challenges and how to select the right microphone
Selected products
- GRAS 146AE
The versatile microphone for almost all acoustic NVH testing. The natural first choice for efficient buzz, squeak and rattle testing - GRAS 42AG
The ideal solution for calibration - GRAS 46BC
The only true multifield, high-sensitivity 1/4" microphone - GRAS 46BL-1
Resources
Buzz, Squeak and Rattle Noise Testing on Electric Vehicles
There is a constant push towards lower masking levels in electric vehicles. At the same time, the demand for less weight increases the design problems when it comes to preventing buzz, squeak and rattle noise.
For buzz, squeak and rattle noise application testing, we recommend GRAS 146AE ½” CCP Free-field Microphone Set because of its extreme versatility and flexibility anywhere in and around the car.
See our complete application offering within electric vehicles here.
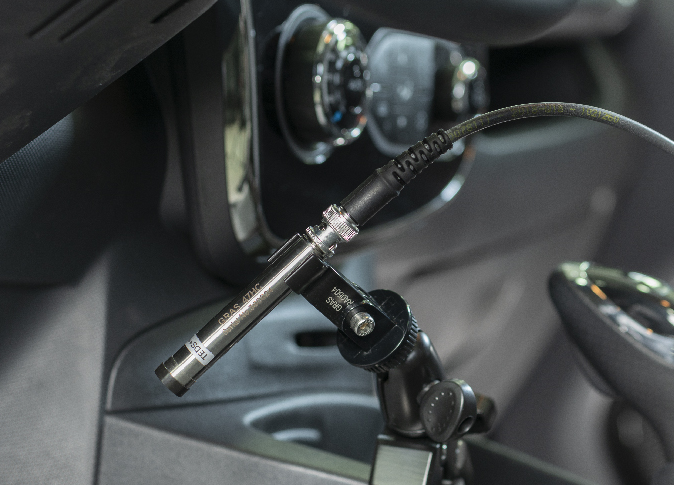
ACOUSTIC TEST TYPES WITHIN BUZZ, SQUEAK AND RATTLE NOISE TESTING
Silent shaker test
Component or system tests are typically performed in a NVH test rig with a silent shaker. A specified excitation profile for the tested parts is used and the loudness in zones is analyzed. This testing is suitable for early verification.
Test track
As soon as vehicle prototypes become available, subjective evaluation of each vehicle is performed on a 4-poster with environmental control and driven on different types of test tracks and under different climate conditions. For long term testing in these extreme environmental conditions, microphones will often be used for recording and later evaluation. The subjective evaluation is supported by a microphone and headphone combination for root cause analysis, often with filtering possibilities, to be able to isolate the problem area. Intensity testing and acoustic cameras are other tools for noise source location.
The tests are repeated after durability testing to ensure minimum degradation.