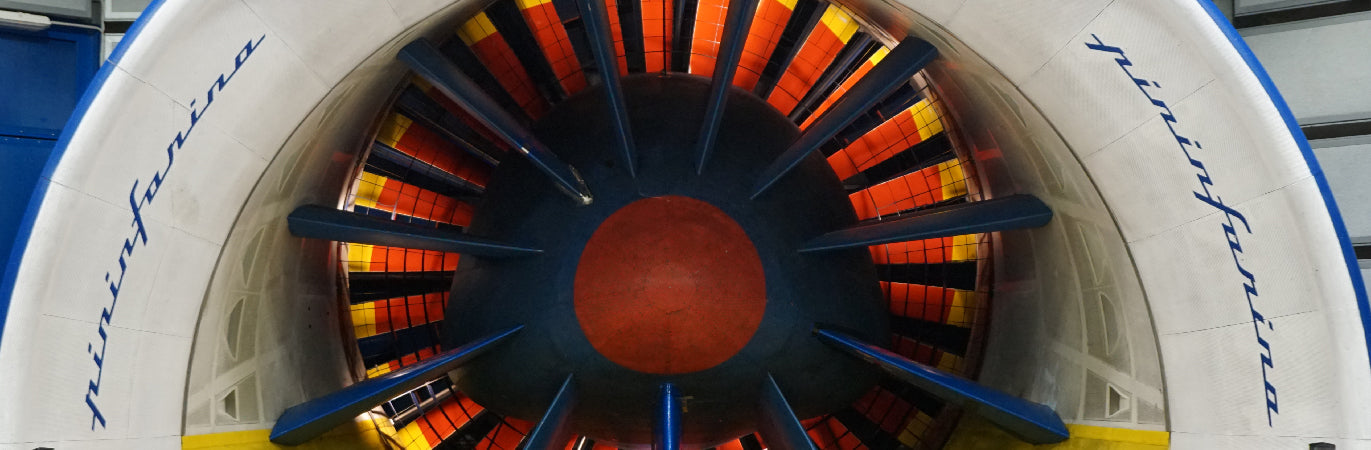
Automotive Wind Noise Testing
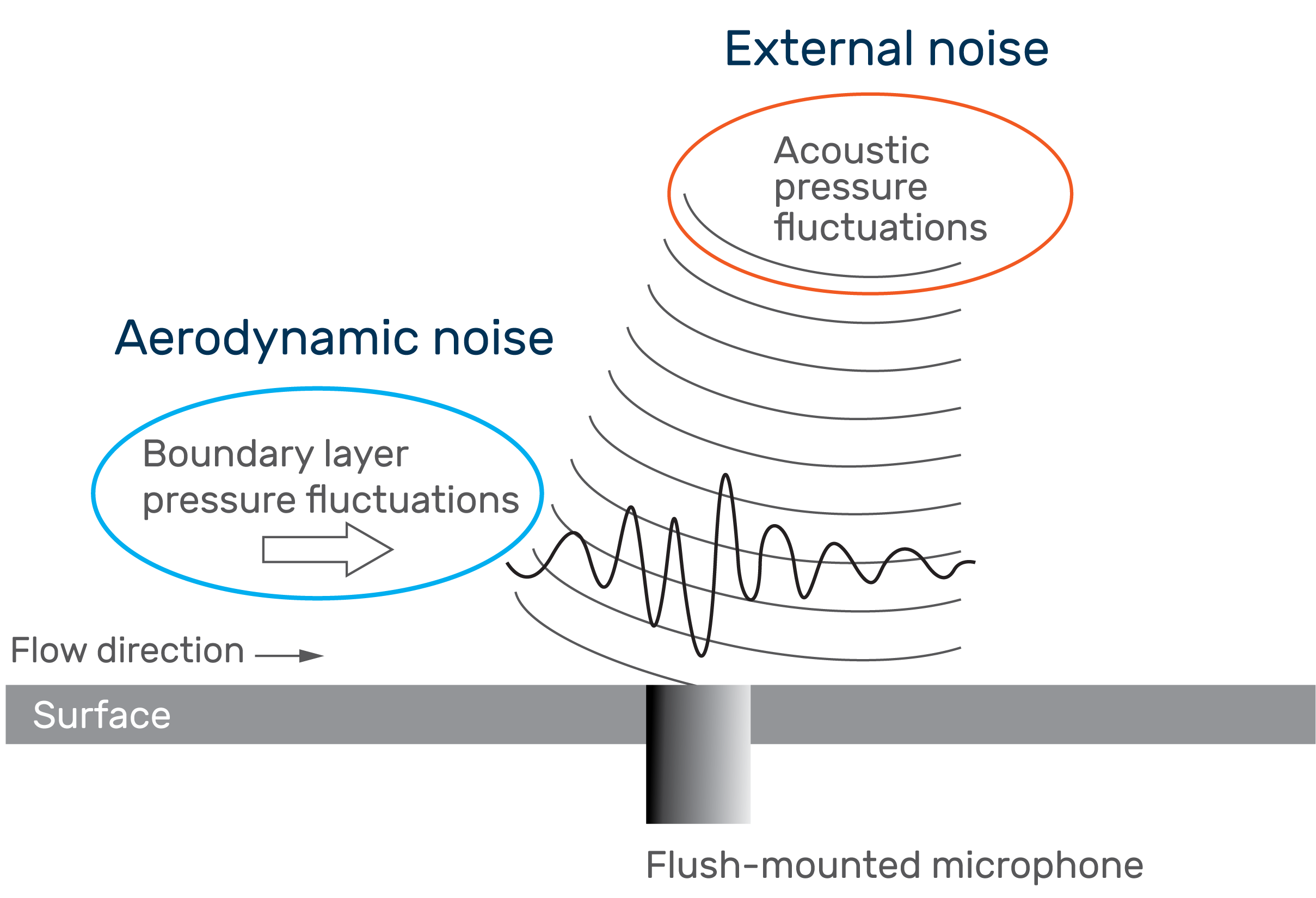
Aeroacoustics is a branch of acoustics that studies noise generation via either turbulent fluid motion or aerodynamic forces interacting with surfaces.
Aeroacoustics is important in the design of vehicles, aircrafts, wind turbines, buildings and bridges to
minimize vibrations and noise.
There are two sources of noise, which are important when talking about aeroacoustics – external noise and aerodynamic noise (or pseudo-noise), see below graphics.
The World´s Thinnest Condenser Microphone >
Measurement Microphones for Aeroacoustics >
Turbulence and Measuring in Boundary Layers >
Selected products
- GRAS 48LX-1
An Ultra-Thin Precision (UTP) surface microphone set for aeroacoustic testing. Ideal for measurements in boundary layers and turbulence. - GRAS 48LX-4 / GRAS 48LX-8
Ultra-Thin Precision (UTP) surface microphone line-arrays for aeroacoustic testing. Ideal for wind-induced noise measurement on vehicles and wind-tunnel testing. - GRAS 40LA / 40LSA surface microphone for mounting on planar and curved surfaces for investigation of turbulence and wind-induced noise.
- GRAS 42AG
The ideal solution for calibration
Resources
The fundamental problems of aeroacoustics is that most test scenarios are expensive and time-consuming and theoretical tests based on calculation software are difficult to simulate realistically. Due to the complexity of boundary layer pressure variations, simulations often require multiple validations and correctional phases.
Specifically, it is difficult to quantify and understand the turbulence and flow-induced noise (boundary layer noise) on different vehicles (aircrafts, cars, drones), simulation tools are slow and imprecise due to the stochastic behavior of turbulence, and experimental tests are costly due to the need for anechoic wind tunnels.
Aeroacoustics is a critical component in automotive vehicle design, certification and operation. Typical wind noise sources are shown below.
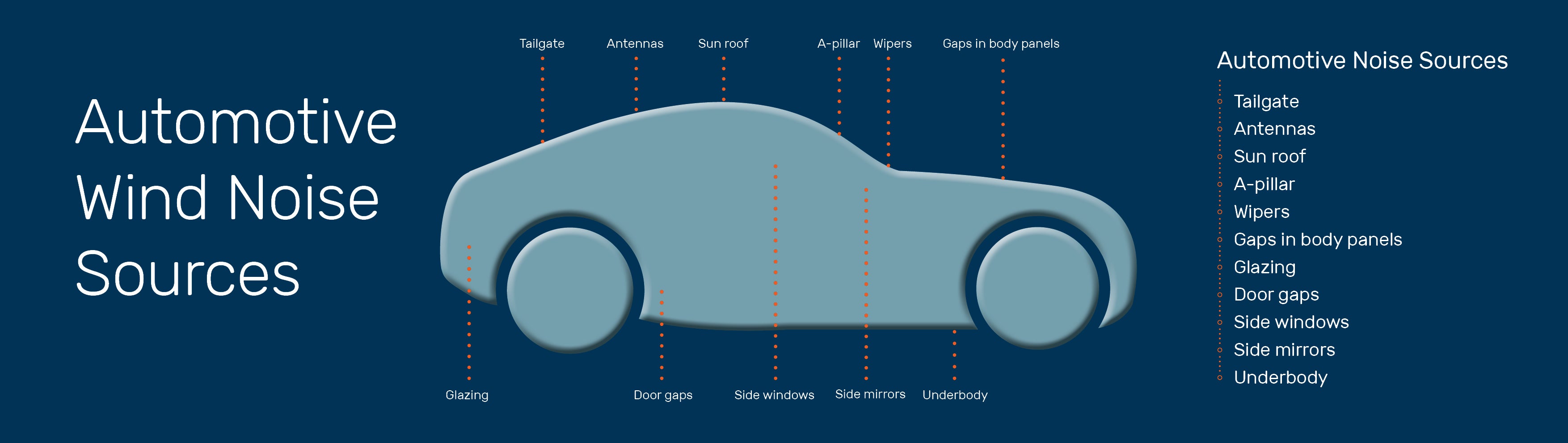
Illustration of vehicle components affecting wind noise.
Read more about our NVH microphones
Boundary Layer Measurements
The main focus of wind noise testing in the automotive industry are measurements in boundary layers. In the automotive (as well as aerospace) industry, these types of measurements are of increasing importance. The main interest is in separating the acoustic signal from the flow-induced turbulent noise. Purposes span quantifying the amount of sound power radiated from a structure, over sound source localization using an array of microphones to quantifying the turbulent stresses to which a structure is subjected.
Boundary layer theory dictates that measurements must be made exactly on the surface of the structure as the statistics of the flow deviate quickly with increasing distance from the boundary. Moreover, care must be taken not to alter the geometry of the structure as such an action may drastically change the flow. See below illustration.
Due to the complexity of measuring boundary layer pressure variations, it is still very difficult to simulate aeroacoustics and often requires multiple validation and correctional phases. Increasing computational power combined with precision microphones from GRAS – allow wind tunnel and on-road testing that help investigate new automotive concepts, verify performance of innovative designs through experimental validations of CFD models, and validate prediction models.
Download our Measurement Microphones for Aeroacoustics brochure.
Discover the new Ultra-Thin Precision (UTP) microphones with an ultra-small form factor,only 1 mm in height.
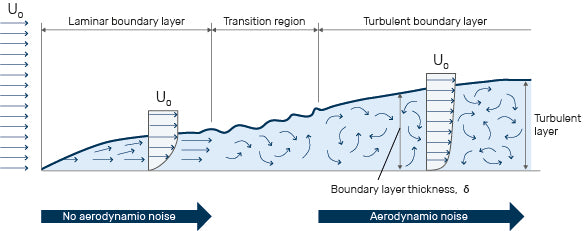
ACOUSTIC TEST TYPES WITHIN WIND NOISE TESTING
Aerodynamic Noise
Vehicle aeroacoustic performance has a strong influence on customer perception and also has importance for safety and comfort. Since flow behavior and noise generation are inextricably linked in any aeroacoustic measurement test, investigations into the flow around a vehicle are important in the field of automotive aeroacoustics.
Wind noise being an aerodynamic noise is actually related to both the body design as well as the turbulence from various components. In relation to the body design, there are three main categories, which affect the aerodynamic noise on a road vehicle: Vehicle form, open cavities and the body sealing. The vehicle form and open cavities are active noise sources, while the body sealing reduces wind noise - depending on the sealing quality.
Likewise, wind noise performance also depends on minimizing aeroacoustic noise sources generated by vehicle components since these all have a direct impact on the measurement of wind noise in the car. As such early concept studies are hugely important as careful design minimizes the problem. Wind noise is, however, often an issue, which is discovered late in the development process. It requires fast and efficient analysis since measures like extended seal systems or sound packages are expensive.
Vehicle Form
Important components related to the vehicle form and design and which have a direct influence on wind noise testing results are A-pillars, side mirrors, windscreen wipers, antenna, underbody and glazing.
Open Cavities
The second major aerodynamic noise source is open cavities. There are two main sources of cavity noise on a vehicle: noise generated by large cavities such as an open sunroof or window - also known as booming or buffeting - and cavity noise from smaller cavities such as door gaps, tailgate and gaps in body panels.
The contribution of wind noise in producing the overall noise heard inside the cabin of a car, however, varies at different speeds. At higher speeds, generally above 100 km/h (approx. 60 miles/h), aerodynamic wind noise tends to dominate the overall cabin noise. This is much more distinct today because the noise from the engine bay and powertrain has been significantly refined and reduced over the years. In today’s electrical vehicles (EV), this problem is becoming ever increasing, since wind noise is one of the most important noise sources for EVs.
Body Sealing
The body sealing as opposed to vehicle form and open cavities is intended to reduce the overall noise heard inside the cabin. Obviously, the sealing quality has a direct effect on the noise reduction. Here the idea is to prevent leaks in the seals around the door apertures and glass. Noise of the sealing systems tends to lead to higher frequency noise inside the cabin, generally above 500 kHz. Depending on make and model, different sealing systems and quality levels are applied.

About
Featured content
Organize content into multiple columns to share useful information to your customers about your products, values...

UTP Microphones – Ultra-Thin Precision Microphones
The GRAS UTP microphones combine the high precision and reliability of GRAS measurement microphones with the need for extremely low-profiled (less than 1 mm) microphones with minimum turbulence influence. With their unique form factor and easy mounting, UTP microphones are specifically designed for in-situ boundary layer testing, when neutral impact and high precision is important. They combine the accuracy of condenser microphones with an extremely small form factor. All LX versions have TEDS.
> High-precision measurement microphones
> Ideal for low-boundary layer testing and confined spaces
> Fast and repeatable mounting with consistent geometry
> Easy in-situ verification
> Wide linear frequency range
> Wide dynamic range
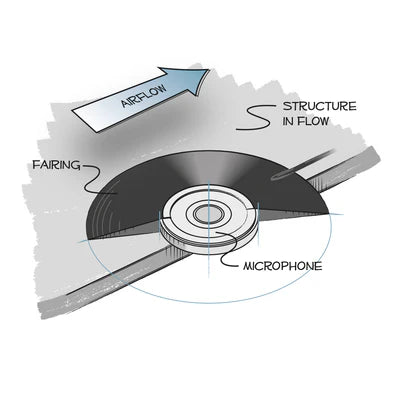
Surface Microphones
The GRAS high-precision surface microphones are designed for in-situ boundary layer testing, where non-invasive mounting is necessary.
They are therefore also well suited for in-flow testing of full-scale objects in wind tunnels.
The height has been kept at 2.5 mm, and a fairing reduces self-generated turbulence.
> High-precision measurement microphones
> Non-invasive mounting and insignificant protrusion
> Integrated preamplifier with plug and measure functionality (TEDS)
> Wide linear frequency range
> Wide dynamic range
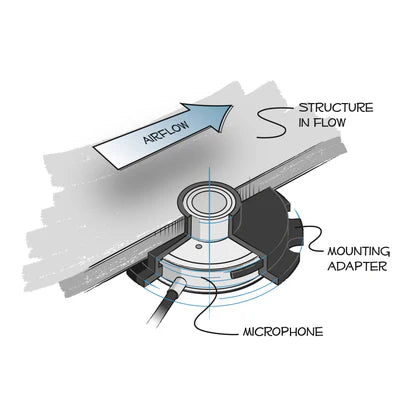
Flush-mount Microphones
This line of acoustic sensors combines the high precision and reliability of GRAS measurement microphones with the need for fitting sensors into very confined spaces and narrow structures.
With an installation height of less than 10 mm, GRAS flush-mount microphones can be integrated into virtually any design without sacrificing aerodynamic properties.
> High-precision measurement microphones
> Very low installation height
> Integrated preamplifier with plug and measure functionality (TEDS)
> Wide linear frequency range
> Wide dynamic range
Wind Noise Testing on Electric Vehicles
Wind noise is an important noise source besides road noise, which is the single most important noise source for EVs/HEVs at speeds above 55 km/34 mph. However, more aeroacoustic testing is required in order to limit this particular noise source.
The amount of wind noise is the same in ICEs and EVs. The difference is that in EVs wind noise makes up a much larger part (30%) of the entire noise exposure because other noises tend to mask wind noise.
As with ICEs, wind noise measurements on EVs can be performed either by using nose cones, wall-mounted microphones or surface-mounted microphones.
Because wind is one of the predominant noise sources in EVs, there is a genuine need to look into new microphone positioning possibilities, which will allow a more comprehensive understanding of noise fields and sources.
GRAS aeroacoustic sensors are an excellent choice, and we recommend GRAS 40LS 1/4" CCP Precision Surface Microphone.
See our complete application offering within electric vehicles here.